Unlocking Maintenance Efficiency: A Guide to Condition-Based Maintenance
February 9, 2024
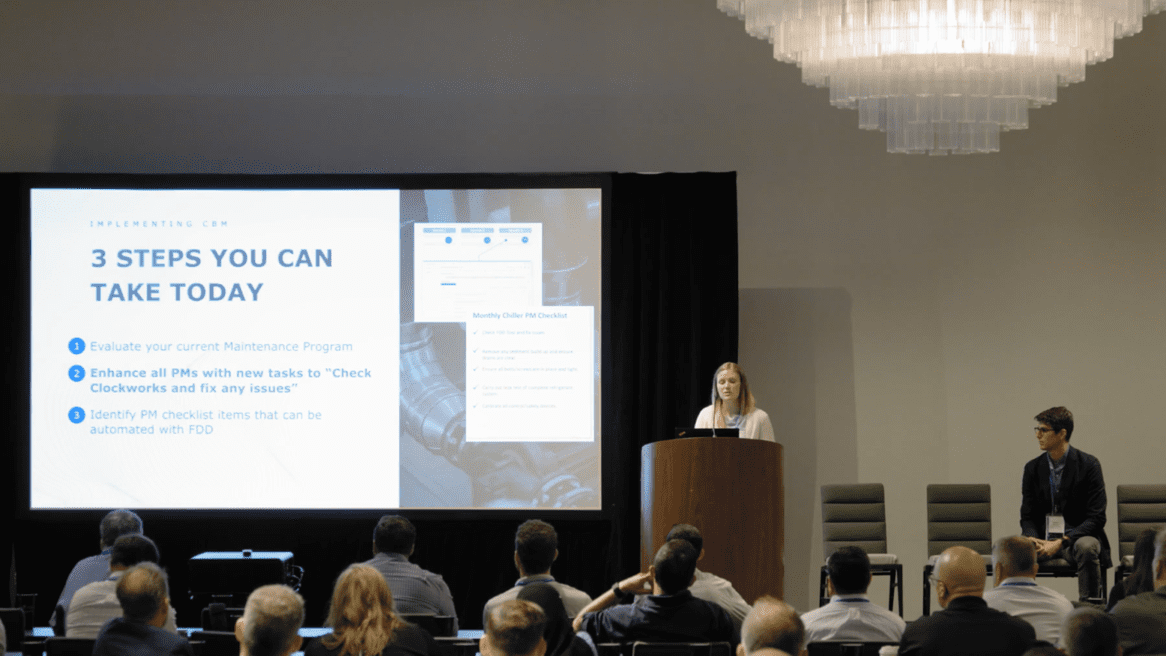
Condition-based maintenance (CBM) is a proactive maintenance strategy that involves monitoring the real-time condition of building equipment to determine when maintenance is needed. While the concept is often discussed conceptually among operations leaders, more and more facility teams are now implementing this proactive approach to maintenance. Shifting to a condition-based maintenance strategy extends equipment life, allows for better budgeting of labor rates, and avoids unexpected downtime. In fact, in two recent pilots with Clockworks clients, a fault detection and diagnotics (FDD) powered condition-based maintenance strategy resulted in a 40% savings in time performing PMs on Air Handler Units.
The nature of facilities management, is reactive. It’s easy to get bogged down responding to equipment breaks, hot/cold calls, and the never-ending back-log of PM’s. Many facility teams struggle with where to start when shifting to a condition-based maintenance program. We often tell clients to start with a crawl, walk, run approach. It’s a swim-lane, and any progress you make toward CBM is good progress!
In this blog post, we’ll break down a recent presentation on CBM and outline a practical three-step approach to implementing it effectively.
Watch the full presentation from Clockworks Analytics’ 2023 Client Summit and learn how Kaiser Permanente and ISS are leveraging FDD-powered condition-based maintenance.
Step 1 (Crawl): Evaluate Your Current Maintenance Program
The first step towards implementing condition-based maintenance is to assess your existing task and work order management approach. Start by classifying your equipment into critical assets, zone equipment, and air handlers, as each category may require a different approach to maintenance. Critical assets like chillers and cooling towers will still require regular preventive maintenance (PM), but the focus should be on leveraging building analytics to enhance the value derived from these tasks.
For zone equipment PMs, evaluate whether these tasks are being completed in a timely-manner and consider alternative maintenance approaches, if necessary. Similarly, assess the frequency and completion rates of PM tasks for air handlers to identify opportunities for improvement.
Step 2 (Walk): Enhance PMs with Fault Detection and Diagnostics
Next, enhance your PM tasks by integrating fault detection and diagnostics (FDD), also known as building analytics software, into the maintenance process. Building analytics software pulls real-time HVAC and building automation system data from across a building or portfolio and automatically calculates potential cost-savings within the platform.
While critical asset PMs should remain intact, there are many PM checklist items that can be automated or enhanced with FDD. First, FDD data arms technicians with a history of performance on the equipment, identifies whether that equipment is actually in need of maintenance, and provides root-cause diagnostics for any current issues. Technicians have all this information at their disposal before they ever head in to do the PM. Sometimes this means avoiding a PM that wasn’t yet needed and sometimes this means being able to streamline maintenance tasks and reallocate those hours to more critical maintenance.
As mentioned, critical PMs on heat exchangers, cooling towers, etc. should always remain in place. But by leveraging FDD, teams can look to the FDD tool to identify any other issues on the equipment that can be fixed along with the PM. For less critical equipment like AHU’s, quarterly PM’s can often be completely eliminated—instead the system will handle those checks—just requiring annual or biannual checks instead.
Step 3 (Run): Implement Condition-Based Maintenance
Finally, transition towards a condition-based maintenance approach where maintenance activities are driven by real-time asset condition data. Utilize FDD dashboards to monitor equipment health and identify potential issues proactively. Instead of adhering to rigid PM schedules, adopt a more strategic approach where maintenance tasks are performed based on asset condition indicators. For example, on equipment where the PM is regularly missed (it might be fan coils, zone equipment, etc.), teams are eliminating that PM and instead monitoring remotely through FDD-powered CBM.

FDD-Powered Condition-Based Maintenance
A condition-based maintenance approach helps lean facility teams prioritize maintenance work orders, spend their time more effectively, extend equipment life, and avoid breakdowns. Building analytics software—and the real-time equipment insights it provides—is a critical part of any modern facility team’s toolkit that wants to shift to proactive maintenance.
Embracing condition-based maintenance is not just a step towards efficiency—it’s a strategic investment in the long-term success of your operations.
Back to blog