Why Should I Run Fault Detection and Diagnostics (FDD) on Zone Equipment in My Building?
December 17, 2024
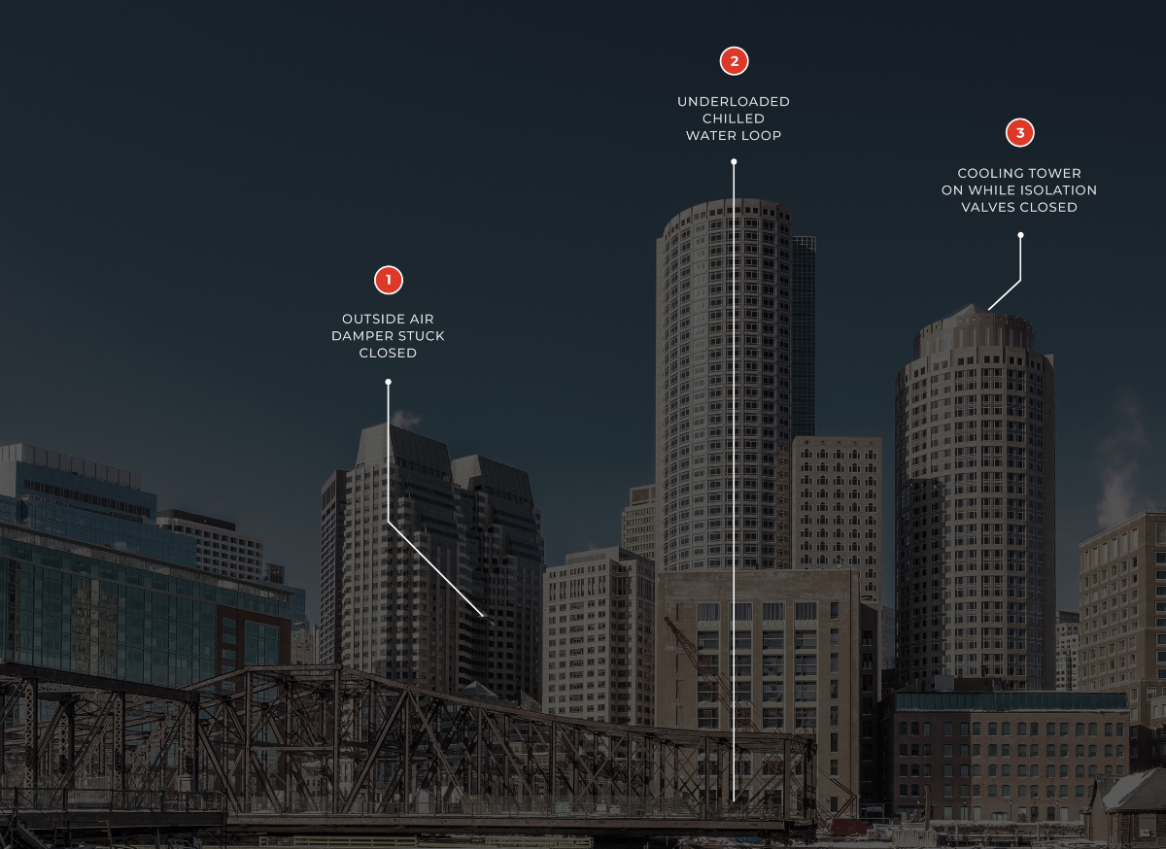
This question inevitably arises as organizations embark on the transformational journey of embedding Clockworks into their facility maintenance workflows.
The question is valid, particularly when considering the nature of zone equipment. Zone equipment comprises small HVAC units that serve individual zones within a building (such as VAV boxes, fan coil units, and radiant heaters). These assets typically have a limited number of points in the Building Management System (BMS) and are controlled in predictable, often standardized ways. Any decent-sized commercial building can contain hundreds, if not thousands, of zone equipment units.
Given such high volumes of relatively simple equipment, it’s natural to question the value that FDD can bring at the zone level. Fortunately, with Clockworks’ global data model currently connecting nearly 300,000 pieces of zone equipment, we can confidently demonstrate the value of implementing FDD on zones.
Building Comfort Performance
Understanding building comfort performance is virtually impossible without running FDD on zone equipment.
Since ASHRAE first published Standard 55 (Thermal Environmental Conditions for Human Occupancy) in 1966, thermal comfort in buildings has been a top priority for building owners and operators. In the subsequent 60 years, best practices for space temperature, humidity, and airflow have become well-established and widely documented.
Creating comfortable spaces relies heavily on data from zone equipment. Sensor points (space temperature), setpoints (occupied heating setpoint), and commands (heating valve position) are all vital pieces of information that inform building operators about comfort performance.
When Clockworks FDD is deployed on zone equipment, operators can monitor comfort conditions more effectively and address comfort-related issues proactively. Through Clockworks’ ability to prioritize comfort-related issues on a scale of 1-10, building operators can focus on addressing the highest-priority comfort challenges in their facilities.
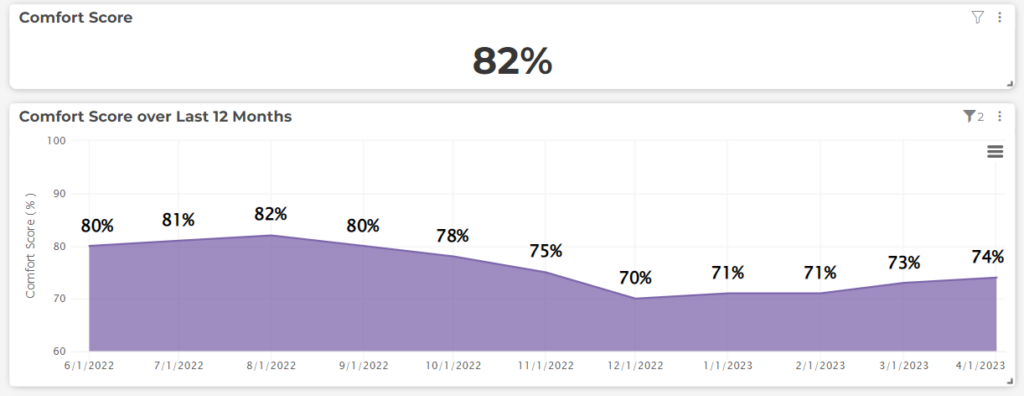
Comprehensive System Diagnostics
Understanding the performance of HVAC systems like heating/cooling plants and air handlers requires FDD deployment at the zone level.
Major equipment such as chillers, boilers, and air handlers are undoubtedly critical to building operations. They represent significant capital and operational investments while providing the primary source of heating, cooling, and ventilation. While some may consider limiting FDD deployment to just these major assets, this approach overlooks a crucial reality: the performance of major HVAC equipment is significantly influenced by downstream zone equipment behavior. Boiler firing rate, chiller staging, and air handler fan speed all depend on downstream zone performance.
Consider this example: An air handling unit’s fan runs constantly at high speed, yet the supply air static pressure remains below its setpoint. Without zone equipment information, identifying the root cause becomes impossible. When zone equipment is included in Clockworks, the source becomes clear—such as multiple downstream VAV boxes indicating stuck-open dampers. These comprehensive system diagnostics become possible only when major system and zone equipment data work in tandem.
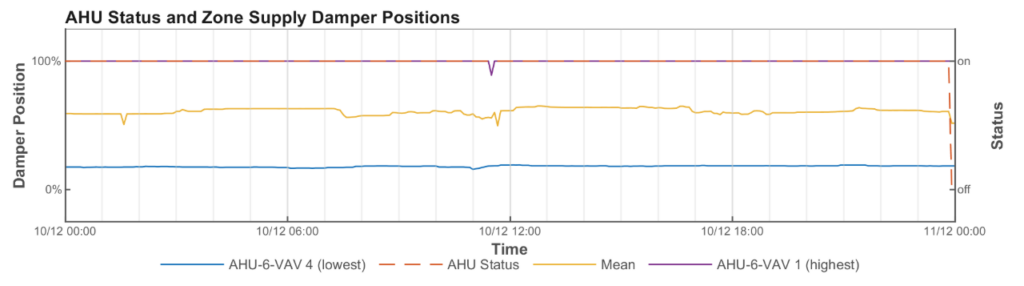
Condition-Based Maintenance
Implementing Condition-Based Maintenance (CbM) strategies on zone equipment significantly increases maintenance efficiency.
CbM represents an exciting evolution in facility maintenance programs. This data-driven maintenance strategy replaces traditional schedule-based task lists. Zone equipment has become the primary testing ground for CbM strategies, largely due to its high volume in buildings. Traditional preventative maintenance task lists for zones are time-consuming and expensive, often resulting in unnecessary maintenance activities.
With Clockworks, facility management teams are abandoning scheduled task-based maintenance on zone equipment entirely. Instead, they rely on Clockworks to determine when and where zone maintenance should occur. This approach allows maintenance staff to focus their time and attention on higher-priority activities.
A recent healthcare client case study demonstrated up to 40% savings in labor hours after implementing a condition-based maintenance approach. The complete adoption of CbM for zone equipment played a crucial role in achieving this efficiency gain. Without including zone equipment in the FDD scope, this transformation to CbM would have been impossible.
Implementing FDD with Zone Equipment
The implementation of FDD on zone equipment represents a fundamental shift in building management strategy. While the high volume and relative simplicity of zone equipment might initially suggest limited returns on FDD investment, the evidence demonstrates otherwise. Through enhanced comfort monitoring, comprehensive system diagnostics, and condition-based maintenance opportunities, zone-level FDD delivers measurable value.
The data from Clockworks’ 300,000 connected zone equipment units confirms that this approach not only improves occupant comfort and system performance but also drives significant operational efficiencies. Organizations that embrace zone-level FDD position themselves to achieve more sustainable, cost-effective, and comfortable building operations while transforming their maintenance practices from reactive to predictive models.
By implementing FDD at the zone level, facilities can unlock the full potential of their building management systems, ensuring optimal performance across all scales of HVAC equipment while reducing maintenance costs and improving occupant satisfaction.
Key Takeaways:
- FDD implementation enables proactive comfort management
- Comprehensive system diagnostics require zone-level monitoring
- Condition-based maintenance can reduce labor hours by up to 40%
- Integration with BMS enhances overall building performance
- Data-driven decision making improves maintenance efficiency
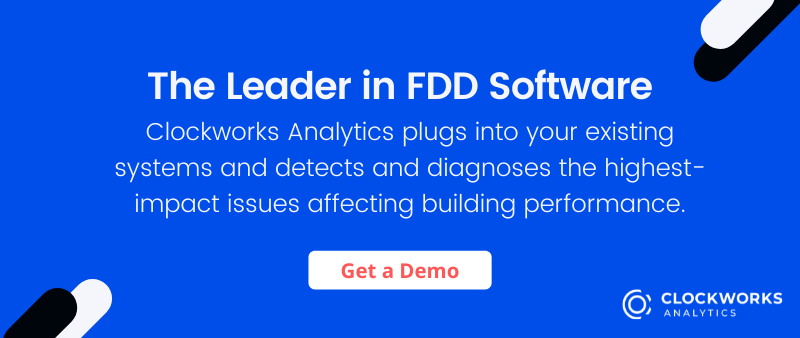