Fault Detection and Diagnostics Whitepaper
May 25, 2021
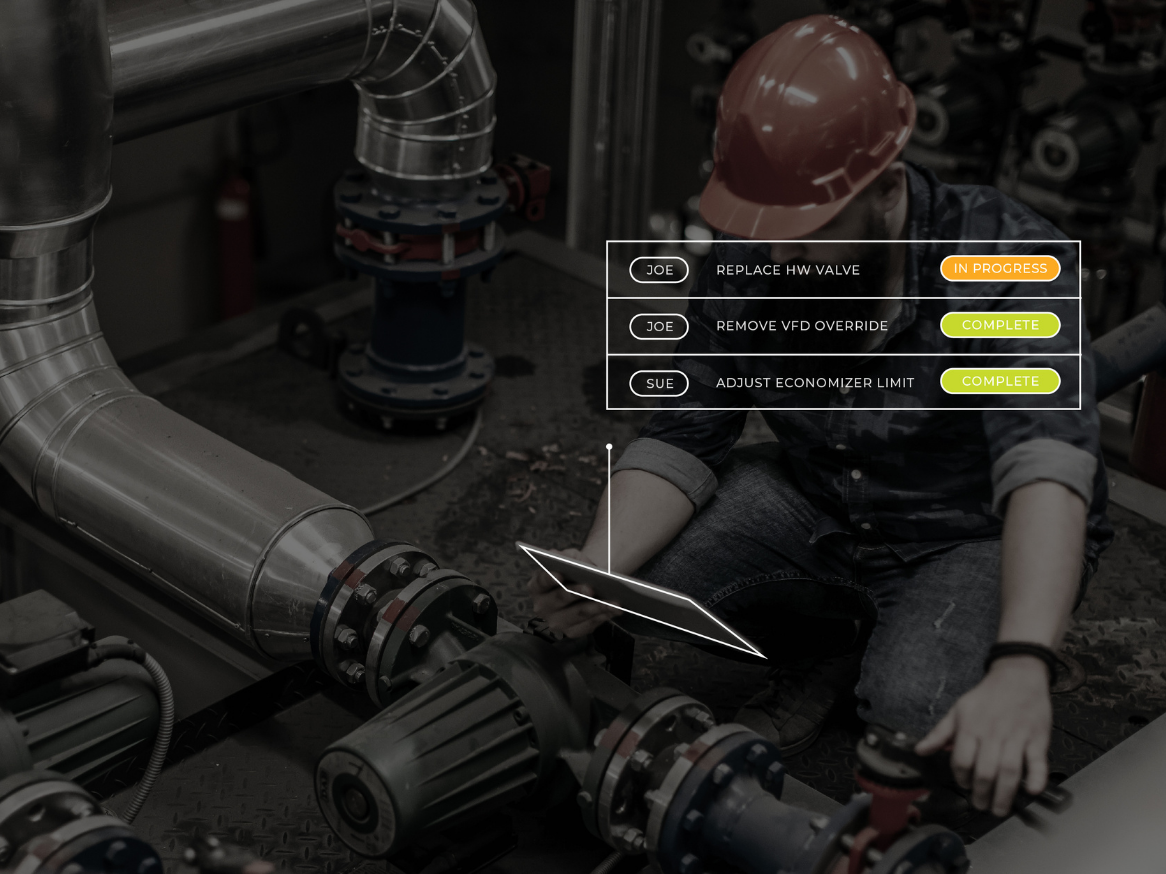
New whitepaper highlights how facilities teams can leverage building analytics to predict repairs, prioritize spend, and save energy.
In a recent study of 6500 buildings by the Department of Energy and Berkeley Lab, The Smart Energy Analytics Campaign, the median organization with a Fault Detection and Diagnostics (FDD) platform saved $3 million annually, or 9% in energy savings. FDD software, sometimes referred to as Building Analytics Software or Energy Monitoring Information System (EMIS), provides a way for owners, operators, and facility managers to proactively manage comfort, system performance, and utility costs. And time and time again, it’s been proven to be the most effective way to reach the promised land of proactive maintenance and achieve the greatest energy and cost savings.
So, why isn’t everyone doing it? Well, it’s not easy. And that’s because we’re using the wrong tools.
A new 16-page white paper from Clockwork Analytics and Nexus Labs, the Building Analytics Comparison Guide, compares the range of tools available to Operations & Maintenance teams. On the spectrum of maintenance—from what is utilized by the most reactive teams to what is utilized by the most proactive teams—those tools look something like this:

DOWNLOAD THE BUILDING ANALYTICS COMPARISON GUIDE
So, what exactly are the differences between the tools above and how can facility teams implement a true FDD system?
Just Say No to Alarm Fatigue
Most facility teams are familiar with a popup that says something like, “Hot Space Temp” with a nice blinking red light on the front end. The problem is, these alarms provide very little actionable information and are usually only slightly less reactive than using no tool at all. They often get ignored. We’ve all seen the BAS with thousands of unacknowledged alarms. Even if you deploy them to their fullest potential, they’re usually only useful for managing and responding to critical equipment issues.
Fault Detection And Diagnostics (FDD)
Making the jump from firefighting to quarterbacking (and achieving real time, cost, and energy savings) requires getting ahead of critical problems. Building fault detection and diagnostics means performing an in-depth analysis that doesn’t just flag an issue, but identifies the root causes of problem so corrective action can be taken. The best FDD tools even recognize related faults and group them together for a clearer diagnosis. But not all FDD tools are created equal. There are actually two kinds of FDD software: those that stop at the first “D” (Detection) and those that go all the way to the second “D” (Diagnostics).
The Building Analytics Comparison Guide tells the story of that second “D” and why it’s so important, illustrated with an example that every facilities team knows well: a large air handling unit, AHU_03, experiencing several issues. It also investigates the three main steps required to fulfill the full potential of fault detection and diagnostics (FDD): analysis accuracy, automated root-cause analysis, and automated prioritization.
